How to reduce forklift accidents? Check out 5 safety tips!
Forklift Safety Tips
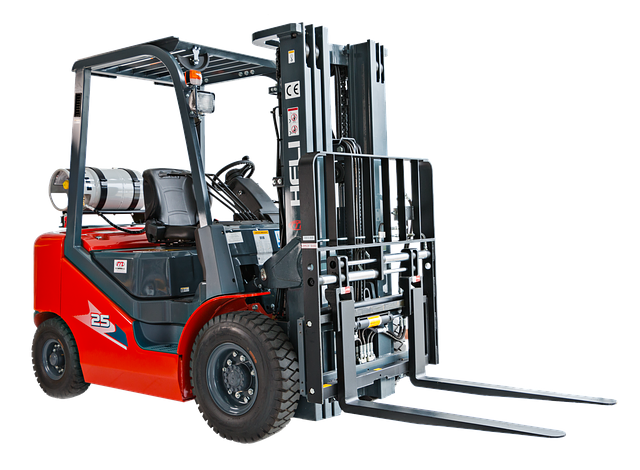
Understanding how to reduce forklift accidents is important, as it is equipment that, if not operated by trained professionals, can become dangerous and cause serious accidents at work, civil and labor claims.
We know that a forklift is a work equipment whose function is to load and unload goods on pallets. The operator, on the other hand, is the professional who is daily exposed to numerous adverse conditions. Thus, for him and everyone around him to be safe, some actions must be put into practice regarding the performance of the activity.
Here are some tips on how to reduce forklift accidents, as well as examples of the most common accidents involving the equipment and what problems your company may face with accidents at work. Good reading!
What are the ways to reduce forklift accidents?
1. Count only on certified operators:
The Regulatory Standard – NR11 establishes safety requirements and specific training for all workers who operate elevators, freight elevators, cranes, forklifts, winches, conveyors, among others.
Therefore, it is mandatory for the forklift operator who after training — and if deemed fit — receives a card containing full name, photo and date of medical examination. It is also recommended that the operator has a National Driver’s License (CNH), as experience in driving a car is essential.
Operators are exposed to hazards on a daily basis and need to be fully aware and responsible when operating the forklift. Putting an unqualified worker to perform this work, in addition to violating NR11, is taking a very large risk.
2. Perform preventive maintenance on forklifts:
It is very important to carry out preventive maintenance on forklifts. Also instruct operators to check the condition of the machine before starting their work.
In daily inspections, check:
- Brakes, steering, clutch, transmission and tires;
- Horn and alarms;
- Control and operation panel indicator lights;
- Safety equipment;
- Hoses, belts and cables;
- Mast and forks;
- Leaks in hydraulic systems or transmission.
In periodic inspections, check:
- Lack of security features;
- Obstructions that block the operator’s vision;
- Screws, pins, nuts and solders;
- Ventilation chains;
- Tilt when load is raised;
- Fork level.
3. Take care of Ergonomics:
The Regulatory Standard – NR17 establishes parameters that allow the adaptation of working conditions to the psycho physiological characteristics of workers, in order to provide greater comfort, safety and efficient performance.
The promotion of ergonomics in the work environment, more than complying with legal aspects, provides benefits for companies. By creating a comfortable and safe environment — ergonomic — you increase productivity and reduce the incidence of accidents.
Still thinking about activities with forklifts, it is important to avoid the following conditions:
- Narrow corridors;
- Obstructions at intersections and doors;
- Disorganized areas loaded with materials;
- Traffic volume on the desktop;
- Ramps with different surfaces;
- Condition of loading dock.
4. Provide regular safety training:
The company must promote regular training to talk about safety measures that must be observed daily, transport of heavy objects, use of equipment and tools, etc.
The operator must make training a regular practice in their daily work routine, aware that safe operation prevents possible damage to the vehicle, their life and the lives of third parties, ensuring the safety of everyone.
However, accidents at work do not only occur due to the forklift operator, but also to pedestrians, therefore, employees who work or circulate in the same environment must participate in training so that safety is guaranteed.
5. Promote safety as part of the organizational culture:
The importance of a safety culture in organizations is fundamental for the prevention of accidents. The work safety legislation is very strict and the fines and punishments applied — to companies that do not comply — by the Ministry of Labor are very severe. Forklift Benefits you must read
Thus, many managers are already realizing that, more than complying with legislation, attention to work safety must be a strategic action with the objective of strengthening the team and promoting the company’s sustainable growth.
What are the most common accidents involving forklifts?
If you do not correctly follow the tips presented above, several accidents can occur during forklift operation. Check out the most common ones below.
Tumble downs:
The tipping can happen due to the negligence of both the operator and the supervisors and managers of the site. This is because a forklift overturns, especially when there is excess weight on the pallets.
In addition, accidents can also occur when reckless maneuvers are performed, due to the driver’s lack of experience or even obstacles on the way. In any case, an overturn can seriously injure both the driver and people around the forklift.
Roadkill:
If falls are complicated situations, pedestrians are even more serious. As you can assume, this type of accident happens when a pedestrian is directly hit by a forklift.
The causes of the incident can be several: distraction, forklift blind spot, lack of signaling, loss of control of the equipment by the driver, etc. Here are different types of forklift
Collisions:
Collisions can happen either against other forklifts or against walls, barriers and pallets. This type of situation occurs a lot due to the blind spot that the equipment has, as well as cars.